Researchers Discover the Key to Safer Batteries Lies on the Surface
By: | March 7, 2019
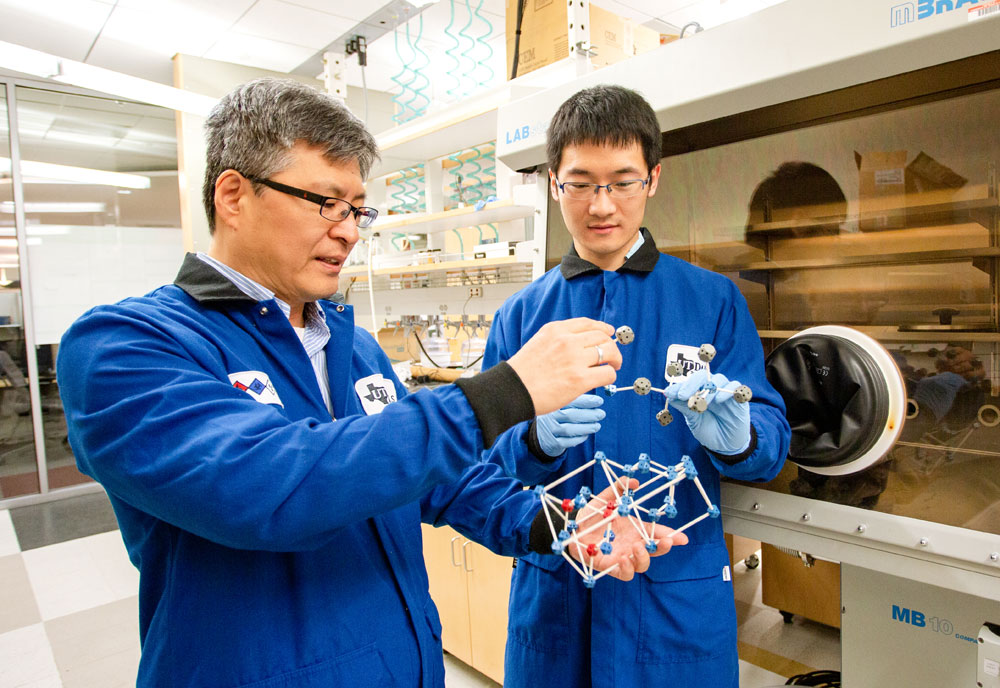
Dr. Kyeongjae “K.J.” Cho (left) and Fantai Kong PhD’17 use atomic structure models of crystalline solid and amorphous oxides to explain the dangers of unstable battery materials. The amorphous model (top) shows the surface oxide coating developed by the researchers.
Everyone wants smaller, cheaper, longer-lasting batteries. Find one that also has greater safety and stability, and you have the Holy Grail of better batteries.
Lithium-ion batteries have been the hands-down favorite for smartphones, tablets, laptops, cameras and rechargeable power tools for decades. But they also have drawbacks, such as “thermal runaway” in which a battery fails — or catches fire — due to the buildup of too much heat.
For years, researchers have been looking for the source of the heat problem and how to fix the associated volatility. After three years of material simulation, synthesis, characterization and battery performance tests, University of Texas at Dallas researchers have discovered that the problem with lithium-ion batteries isn’t inside the battery materials.
“It turns out only the surface of the battery cathode materials is the problem,” said Dr. Kyeongjae “K.J.” Cho, professor of materials science and engineering in the Erik Jonsson School of Engineering and Computer Science. “The inside is OK. This gives us great hope we can figure out how to stabilize the surface and make really high-capacity batteries a reality.”
“This gives us great hope we can figure out how to stabilize the surface and make really high-capacity batteries a reality.”
Dr. Kyeongjae “K.J.” Cho, professor of materials science and engineering at UT Dallas
Cho and his colleagues described their findings in the Jan. 10 print edition of the journal Advanced Energy Materials.
Cho said high-energy-density batteries come at a high price: increased volatility.
“When a battery is constantly charged and recharged, the material begins to degrade. Released energy causes heating, and the battery catches fire. That’s essentially the safety problem,” he said.
The good news?
“Only the surface of the battery materials is unstable and unsafe. If that can be addressed, it can be fixed,” he said.
During the constant cycles of charging and recharging, oxygen gases are released from the surface of battery materials. During that process, the pathway for lithium-ion transportation from the interior to the exterior can get blocked by metallic nickel dust, which is generated along with gas releasing, Cho said.
“When there is a blockage, there’s no way to transfer lithium-ions at the surface that want to come in and out. This leads to rapid decrement of battery capacity. As the amount of heat increases, the chances of fire and explosions also increase,” he said.
That simple, yet profound, discovery at the surface of the battery materials might change the way manufacturers build them. Cho suggests perhaps a well-designed oxide coating could be added on the battery surface.
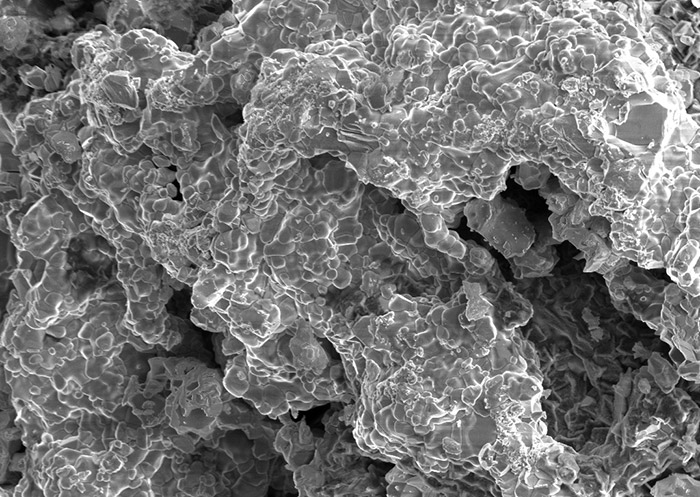
This image from a scanning electron microscope shows the surface of battery material powder that was part of the researchers’ study.
“Modifications could lead to maintaining a charge for a longer period of time,” Cho said. “This is the problem industry is trying to solve right now for the next generation of lithium-ion battery. It’s very exciting, and we are working on the next stage.”
Fantai Kong PhD’17, lead author of the study and Cho’s former student, is a senior engineer with Hunt Energy Enterprises in Dallas working on large-scale energy storage and material projects. He said solving the heat problem in batteries could lead to a 20 percent to 30 percent higher capacity.
“We are right at the threshold of commercial viability. There could be a commercial product in a few years,” Kong said.
Based on the new findings, Cho said there is some industry interest in working with the UT Dallas group on next-generation cathode materials for electric vehicle batteries. Cho’s group also is collaborating with the U.S. Naval Research Laboratory on a follow-up research project to increase the capacity and safety of cathode materials.
Other UT Dallas researchers who contributed to the study are: Yongping Zheng PhD’18; Sahila Perananthan PhD’17; Dr. John Ferraris, professor of chemistry; and Dr. Moon Kim, professor of materials science and engineering and the Louis Beecherl Jr. Distinguished Professor. Dr. Chaoping Liang, Dr. Roberto C. Longo and graduate student Luhua Wang, former members of Cho’s lab, also contributed to the study.
The work was supported primarily by the government of South Korea and L&F Co. of Korea.
Media Contact: The Office of Media Relations, UT Dallas, (972) 883-2155, newscenter@utdallas.edu.